Let us take you back 32 years. Love was in the air, hope was on the horizon – the ‘60s were in full swing. Keith Rawkins – a fine art graduate, who had spent several years working alongside ‘The mad silkman’ Zika Ascher – spotted an opportunity. London’s fledgling fashion houses were in need of fabrics. So Keith and his wife Stephanie began designing and hand-printing from their basement flat in Fulham. Before long, they were supplying some of the city’s most celebrated couturiers. Marina Mill was born and is today creating a bespoke series of fabrics unique to Chelsea Barracks.
Today, much has changed. In the mid-70s, a handful of commissions for private residences and boutique hotels shifted the firm’s focus away from fashion; as the industry became increasingly ‘fast-paced and cut-throat’, Marina Mill made the decision to concentrate exclusively on interior design. It undertook bespoke projects and found a new home in a Victorian mill on the banks of the River Medway. As a company, it has travelled a long way.
Yet comfortingly, two fundamental aspects of Marina Mill remain constant: the family-run ethos, and the company’s steadfast commitment to hand-crafted fabrics. Keith and Stephanie may have retired, but the business is carried forward by their children, Guy and Tandine.
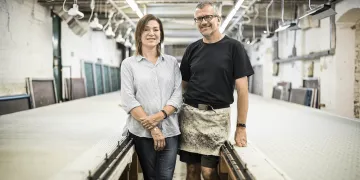
‘We’ve always got on really well,’ explains Tandine when we meet at the company’s home in Kent. ‘Guy is the managing director so he oversees everything. I’m design director – so I handle the creative side. I do the drawing, the artwork and colour separation for all new designs.
Sometimes I have to create a design from scratch; sometimes a client will come to us with an old fabric they found in a market somewhere that they want us to reproduce.’
Behind Tandine, print tables stretch into the distance like slender bowling alleys. ‘We found this building, because we needed the length for the long print runs,’ she explains. Unlike most of their competitors, Marina Mill has consciously abstained from modernization. ‘We’ve kept it traditional because we see such beauty in it. The vast majority of fabrics are digitally printed, or machine printed certainly. Our process is very time consuming, but it gives a special look. You get subtle variation of colour depth and texture all along a length of fabric – it gives it life, which digital isn’t able to do in the same way.’
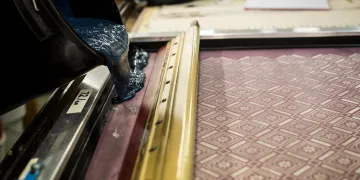
The stunning results of this process speak for themselves. The team at Albion Nord were blown away, and enlisted Marina Mill to print the two fabrics they have designed for the Chelsea Barracks Collection. Yet, bringing the designs to life was a laborious task. ‘There are lots of processes involved,’ Tandine reflects. ‘To make the screens you have to go through the artwork process. That gets engraved onto the screen, and coated with a light-sensitive emulsion. Then, we have to roll the chosen base-cloth on these tables. It’s stretched and pinned tight so it’s absolutely taut, because you have to eliminate any movement in the fabric. Each design has its own repeat distance, and you have to set the stops on the rail to the exact distance of the repeat. One of the lads on the railside poors in the ink, chooses the right squeegee for the job and then pushes the ink across the screen, passing it to the guy on the other side. He does the same – passes it back, so it’s two strokes. Then they lift the screen, and move it up the table.
They print every other repeat first, that has to dry before they can fill in the gaps, because the screen frame overlaps. They turn the heaters on, dry it, come back, fill in the gaps and that’s done.’
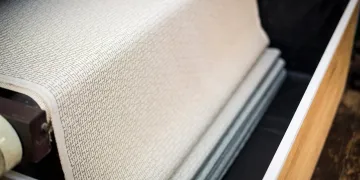
This truly is a bespoke process – but Marina Mill doesn’t stop there. The firm also employs expert colour mixers to blend eco-friendly paints by eye, ensuring that every client receives something totally unique. Albion Nord opted for heritage colours to reflect the Georgian theme running through the Barracks. For the diamond design – a reinterpretation of a tile in the Garrison Chapel – they chose an indigo blue; the spindle design – which draws inspiration from the floorplan of the Royal Chelsea Hospital – comes to life in a gorgeous olive green.
Though this was a herculean task, it was one Tandine clearly cherished. ‘Chelsea Barracks have ordered 80 metres each of the two designs,’ she tells us. ‘One of the designs is on a chunky, heavier-weight linen suitable for upholstery, whereas the other one is on a lighter-weight drape linen. They’ve got quite different usages. The diamonds would look fabulous on big sofas, the other design, as curtains or blinds, would work really well.’
Marina Mill’s part in the project may be done, but Tandine is already looking towards the future. ‘The screens are now made, so we would love to work on developing other colourways. It’s nice to work on a special project like this. It’s such an iconic development – it’s great for us to be able to talk about being involved. It’s nice to be appreciated for our part.’
Indeed, it would be hard for anyone to overlook such majestic fabrics. And once the Townhouses are completed, they will become a vital part of peoples’ homes – destined to be appreciated for decades to come.
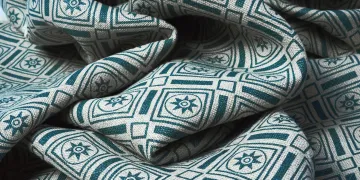
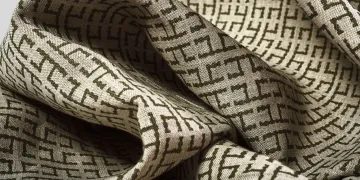